How Packaging Machine Repair Can Boost Your Production Output
How Packaging Machine Repair Can Boost Your Production Output
Blog Article
The Ultimate Guide to Packaging Maker Fixing: Maintain Your Operations Running Smoothly
Understanding the details of product packaging device repair is crucial for keeping ideal performance and minimizing disturbances. Regular maintenance not just expands the life of these makers yet likewise addresses common concerns that can hamper efficiency.
Significance of Normal Maintenance
Regular upkeep of packaging equipments is critical for making sure optimal efficiency and longevity. By applying a structured upkeep routine, drivers can determine potential problems prior to they intensify right into considerable troubles. This positive strategy not only decreases downtime but additionally extends the life expectancy of the equipment, eventually leading to minimized functional costs.
Routine inspections enable the assessment of essential components such as seals, sensing units, and belts. Attending to damage promptly stops unanticipated failures that might interfere with manufacturing and lead to expensive fixings. Additionally, routine maintenance assists make certain compliance with industry requirements and guidelines, cultivating a safe workplace.
Additionally, upkeep tasks such as lubrication, calibration, and cleaning substantially improve equipment performance. Boosted efficiency translates to consistent product quality, which is important for preserving client fulfillment and brand track record. A properly maintained product packaging maker runs at ideal rates and minimizes material waste, contributing to overall productivity.
Common Packaging Equipment Concerns
Product packaging makers, like any type of complicated machinery, can encounter a variety of usual concerns that might impede their performance and efficiency - packaging machine repair. One widespread trouble is inconsistent sealing, which can lead to item wasting and waste if packages are not properly secured. This commonly results from misaligned components or used sealing elements
An additional constant problem is mechanical jams, which can occur as a result of foreign objects, used parts, or improper placement. Jams can trigger hold-ups in manufacturing and increase downtime, inevitably impacting overall performance. Furthermore, digital malfunctions, such as failing in sensing units or control systems, can lead and disrupt procedures to incorrect measurements or irregular maker behavior.
Furthermore, issues with product feed can likewise arise, where products might not be delivered to the product packaging area regularly, causing disturbances. Finally, damage on belts and rollers can bring about suboptimal performance, calling for immediate interest to avoid additional damage.
Understanding these typical concerns is important for preserving the honesty of packaging operations, making certain that machinery runs smoothly and successfully, which subsequently aids in meeting production targets and preserving item quality.
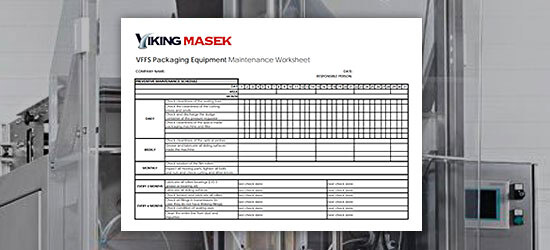
Repairing Methods
Effective troubleshooting strategies are necessary for quickly addressing concerns that develop with packaging equipments. A methodical approach is essential for determining the origin of malfunctions and decreasing downtime. Begin by gathering details regarding the symptoms observed; this may consist of unusual sounds, operational hold-ups, or error codes presented on the device's user interface.
Next, describe the device's guidebook for fixing standards particular to the version in question. This source can provide useful understandings into usual issues and suggested analysis steps. Use aesthetic evaluations to examine for loose connections, used belts, or misaligned components, as these physical aspects often contribute to functional failings.
Execute a procedure of removal by testing private maker features. For instance, if a seal is not developing appropriately, assess the sealing system and temperature level setups to determine if they satisfy functional requirements. Record each step taken and the results observed, as this can aid in future fixing efforts.
Repair service vs. Substitute Choices
When encountered with tools breakdowns, determining whether to fix or change a product packaging machine can be a complex and critical selection. This choice depends upon a number of essential elements, including the age of the machine, the level of the damages, visit their website and the forecasted effect on operational performance.
To start with, think about the device's age. Older machines might call for more constant fixings, causing higher advancing expenses that can go beyond the investment in a brand-new system. Furthermore, examine the intensity of the malfunction. Small problems can typically be dealt with quickly and cost effectively, whereas comprehensive damage could require a significant monetary commitment for fixings.
Functional downtime is another vital consideration. Investing in a new maker that offers enhanced effectiveness and integrity might be much more sensible if fixing the machine will create long term delays. Take into consideration the schedule of components; if replacement components are difficult to come by, it may be a lot more critical to change the machine entirely.
Ultimately, carrying out a cost-benefit analysis that includes both lasting and prompt effects will certainly assist in making an educated choice that straightens with your financial restraints and functional objectives. (packaging machine repair)
Preventative Actions for Long Life
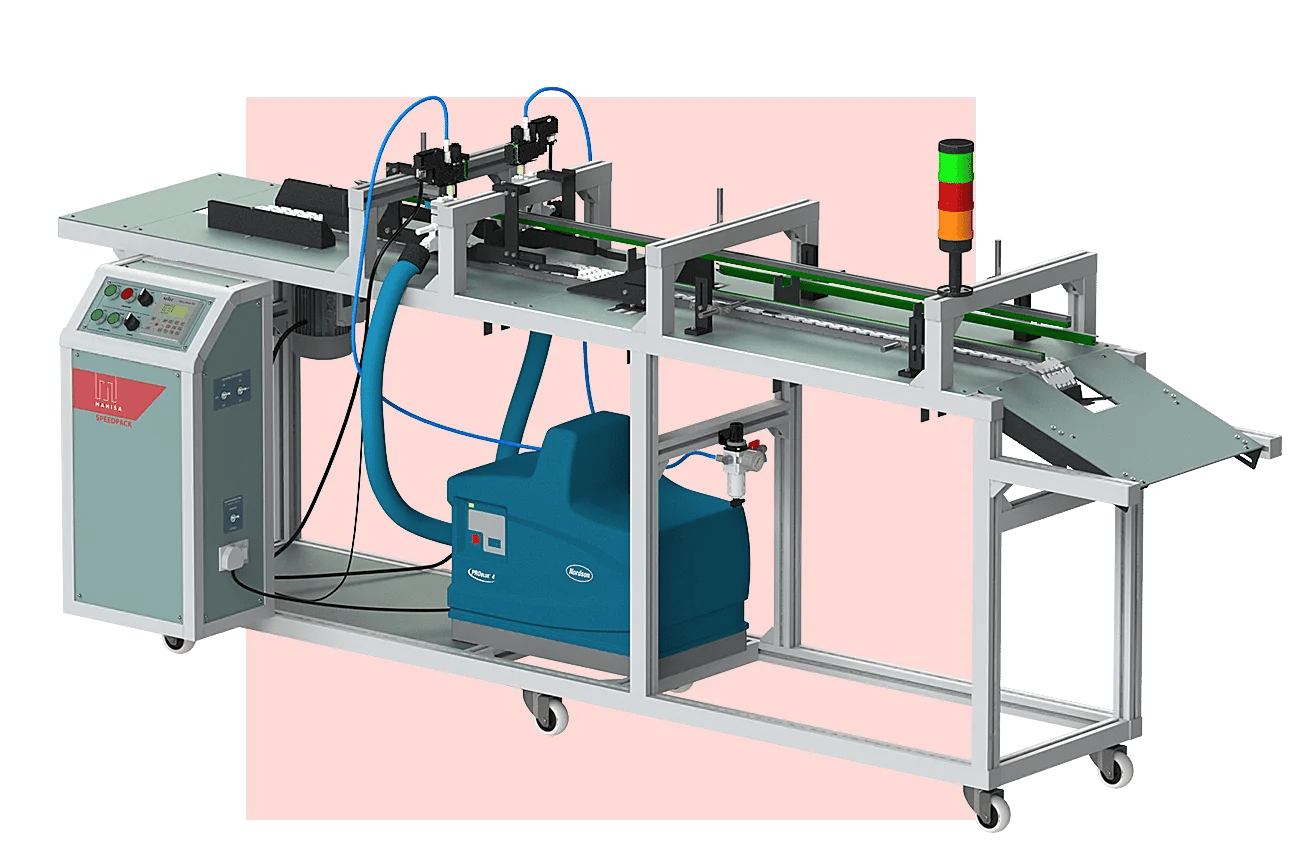
Key precautionary procedures consist of routine lubrication of moving parts, positioning checks, and calibration of sensing units and controls. Establishing a cleaning routine to eliminate particles and impurities from equipment can considerably minimize damage (packaging machine repair). In addition, monitoring operational parameters such as temperature and vibration can assist find abnormalities beforehand
Educating team to recognize signs of wear or malfunction is another essential component of preventive maintenance. Empowering operators with the knowledge to perform basic troubleshooting can lead to quicker resolutions and minimize operational interruptions.
Documentation of upkeep tasks, consisting of service records and evaluation findings, fosters liability and promotes educated decision-making pertaining to replacements and repairs. By focusing on preventative procedures, services can ensure their packaging equipments run at peak performance, ultimately bring about boosted efficiency and decreased functional prices.
Final Thought
In conclusion, the reliable repair and maintenance of packaging makers are vital for sustaining operational performance. Routine maintenance minimizes the danger of common concerns, such as inconsistent securing and mechanical jams, while methodical troubleshooting techniques assist in prompt resolution of breakdowns. Mindful consideration of fixing versus replacement choices contributes to economical management of resources. By applying precautionary actions, companies can boost machine durability and ensure continuous informative post performance in packaging operations.
Recognizing the details of packaging device repair work is critical for maintaining optimal performance and reducing interruptions.Routine upkeep of product packaging equipments is important for making certain optimum efficiency and long life.Product packaging equipments, like any kind of complex equipment, can encounter a variety of common issues that might prevent their efficiency and performance. If fixing the maker will certainly trigger extended delays, investing in a new equipment that supplies boosted performance and integrity may website link be a lot more prudent.In conclusion, the effective upkeep and fixing of product packaging devices are critical for sustaining functional performance.
Report this page